Because of Stability and Simplicity
In mechanical design, there is a fundamental principle: the simpler and more stable a structure, the harder it is to replace. This simplicity and stability are also reflected in lower material requirements.
For example, in transmission systems, spherical gears for universal drive were proposed long ago, but remain theoretical models without industrial-scale application.
Why?
Because no reliable, durable material exists to withstand the wear required for sustained industrial use.
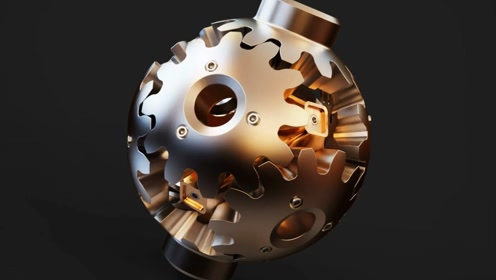
Similarly, flathead screws demand the lowest material strength. Cross or star-shaped screw heads, with more grooves, face higher risks of tooth wear or deformation due to uneven stress distribution.
Simple components also require minimal tooling: flathead screwdrivers are the easiest to manufacture or improvise (even with a coin), and damaged or rusted screws can be temporarily repaired by deepening the slot.
Notably, many cross screws retain one deeper groove to allow dual compatibility with flathead tools.

Devices like subway systems and smartphones use specialized screws primarily to deter tampering, while flathead screws—easily opened with a coin—embody ultimate simplicity.
Though flathead screws appear to save just one manufacturing step compared to cross screws, the latter require precise alignment of intersecting grooves (angle tolerance ±3°) and central positioning, significantly increasing costs and complexity.
In all mechanical systems, the simplest and most primitive structures often prove the most reliable and enduring. Conversely, intricate designs tend to elevate failure rates—a universal law of engineering efficiency.